5Sの実践
製造現場にて
製造現場=モノ作りの場で5Sを進める際に意識すべき事は、現場でよく言われる4M(Man:人、Machine:設備、Material:材料、Method:方法)、場合に因っては測定=Measurementを加えた5Mが大事になる。ただ、5つ目のM=Measurementは測定機器をMachine:設備、測定方法、機器の使用についてはMethod:方法に含まれる。シンプルにしたいので、この章では4Mで進めたい。4Mについては別の機会に改めて書きたいと思うが、モノ作りの場では4Mが無ければ生産活動は成り立たない。5Sを行う際、現場を4Mの観点から分けて見れば作業は進め易い。生産活動に求められるのは、必要最小限の資産(資源)でアウトプットし、効率よく利益を上げる。効率を上げる為にムダの排除は必須であり、如何に達成するか試行錯誤を繰り返す、それらを改善活動と称するが、そのカギを握るのが5Sであると考える。
1.Man:人
人に付いて述べると、整理=人員整理、解雇、整頓=整列、清掃=身の回りの掃除、清潔=身だしなみ、躾=育ち、家柄という感じでしょうか。清潔、躾はその人となりがよく現れ、顔立ち以上にその人の特徴が見て取れる感じがします。モノ作りの場に於いて、「整理」は5Sの中でも重要なポイントになります。整理というと良いイメージが湧かないようであれば「省人化」「省力化」に置き換えるという方法も有りだと考えています。
工程表に則り10人で組立てを行っていると仮定します。工程表が正しいと思い漫然と続けるのではなく、5Sの観点からムダな作業、工程は無いか、モノの配置は適切か、設備・装置に汚れがありその影響で停止することは無いか、作業者は指示された事を守っているか等を精査し、欠点が有れば是正、欠点が無くとも最適なのかという疑問を持ちムダと思える作業、工程、環境の改善を図る。省人化が難しい場合は、人の代わりにロボットに置き換えられないか。工程内で組立作業を完結させる事が効率的なのか、工程外で一部組立てたらコスト、効率がどうなるのか。とにかく作業者数の最小化を目指して改善内容を検討する。当然ながら費用対効果を見過ごしたのでは意味が無い。
気持ちの良い工場というのは、整理・整頓・清掃が行き届いていて、話し声が少なくムダに人が歩いていない、作業時に発する音しかしないという所でしょうか。また、決められた服装を決められた方法で着用しているかである。着衣に油脂類が付着し汚れている、ボタン、ファスナーが閉められておらず、袖、襟元が開いている、着帽を義務付けられている職場で無帽、上げるとキリがありませんが、一見して着衣が乱れている職場は、当然ながら5Sに消極的で品質、納期に問題を抱えている。
5Sをやる意味が周知され、一人一人が自覚を持って実行している、習慣化させるまで大変ではあるが、経営者、管理者が諦めずに文化と言えるまで取組む事が大事である。諦め、妥協が有れば5Sは中途半端であり、緊張感の欠ける無気力な会社になる。とはいえ、世の中5Sがうまく行ってなくても人間関係、利害関係で成り立っている事の方が多い。審査、監査で厳しい評価を下されても、トップが使うと決めれば、嫌でも調達先として使わなければならない。理想と現実の乖離である。
モノ作りの現場に於いて、人に対する5Sは省人化、省力化を意識して進めるべきである。一つの工程で省人化により減らした人員は、他の工程に充てるか新規事業展開での活用が期待出来る。
余談になりますが、5Sが出来ないのはどのような人か経験から言えば、業務メールの未読が多い人。受信トレイに8時間以上経過した未読の数が1件でもあれば、職場、身の回りの整理すら出来ない人と言える。言葉を選ばず言うなら仕事が出来ない部類である。書類、見積り等納期当日慌てて作業を始める。事前に遅れる連絡をするならまだ良い方で、一日の遅れはセーフだと言うのも居る。影響が社内に留まるなら、まだやりようもあるが、取引先にも同じことをやらかす。当然信頼関係を築けるはずも無く。
現役の頃ピーク時で一日200件を超えるメールを受け取ることがあった。社内各部門のスタッフが100人程居たので、その数は普通と言えば普通であり、管理者として判断しなくてはならないメールはその内10件もあれば良い方。半数以上はCCで送られたもの。言っては申し訳ないがどうでもいい内容であった。メール処理は必要なフォルダーを作成し、自動仕訳機能使えば短時間で効率的に処理出来る。未読の多い人はこういったツールを利用出来ていない場合が多い。自動仕訳に限らず、持っている機能をどのように使うか、それに因って5Sの成果に差が出る。
2.Machine:設備
次に設備であるが、動力を用いた装置・設備に限らず、電線を切る、曲げる工具(ニッパー、ペンチ)、小さな部品をつまむピンセット等生産する上で必要な工具、治具までをMachine:設備に含まれます。これらの5Sはやり方に因って、思った成果を上げられずに頓挫する事もある。推進する関係者、現場の作業員にとっては真価を問われる対象でもある。
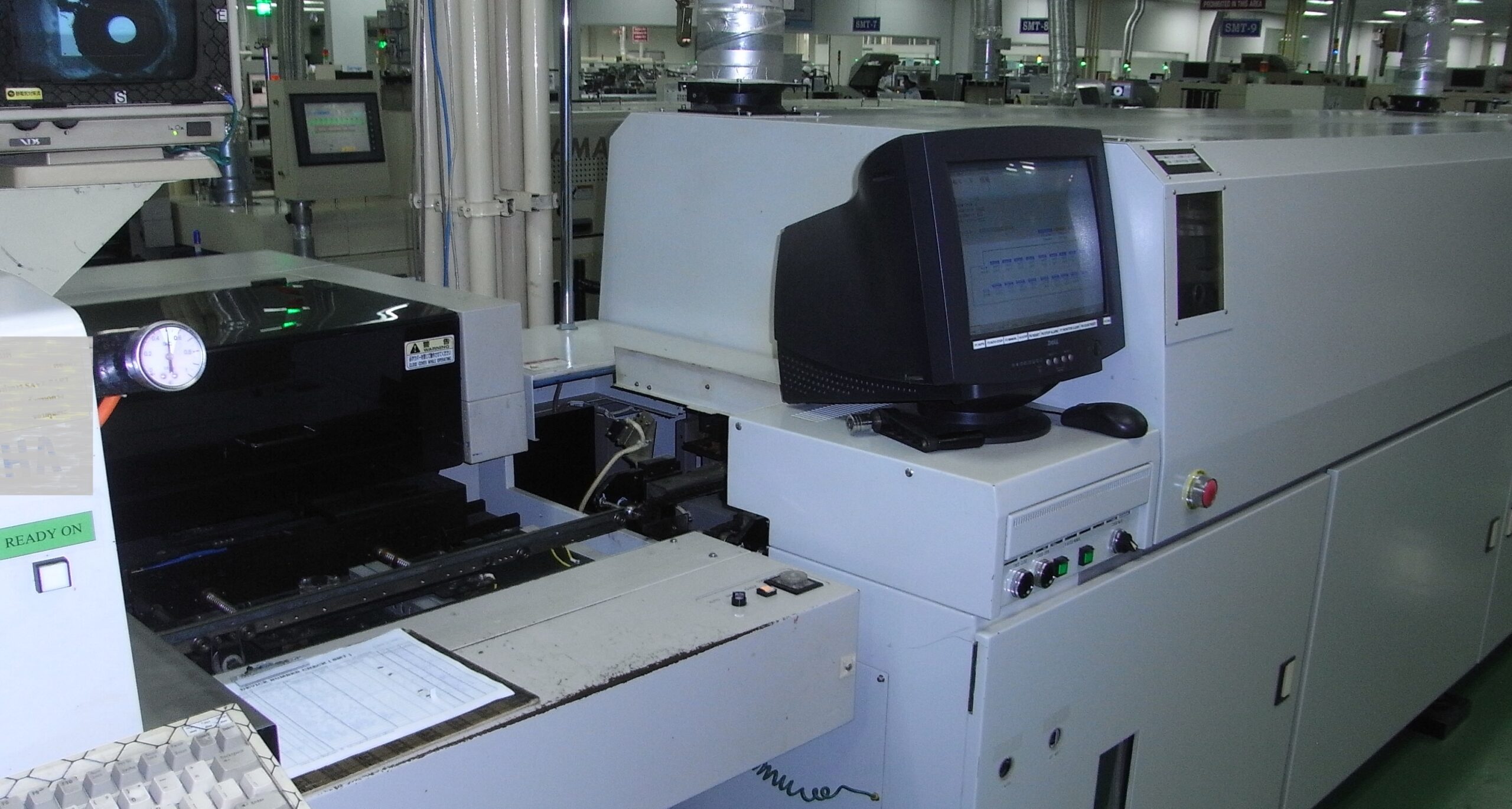
Exif_JPEG_PICTURE
整理:要るモノと要らないモノを分け、要らないモノを捨てる。
大型の設備、装置は簡単に移動出来ない様に、床など建物に固定している場合が多い。数年先まで稼働出来る計画が有れば、現時点で動いていなくても、設置しておくのは常だと思う。しかし、過去に主力生産機種の為に設置した設備でも、稼働頻度が低くなればむしろ邪魔な存在となる。現状の主力生産機種に合わせたレイアウト、動線確保は重要であり移動を検討すべきである。生産機種は市場ニーズの変化に因り短期間で入れ替わる事が多い。変化に応じたレイアウトと動線変更は常に最適化するため変えるべきであると考えた方が良い。その中で要らないモノとして廃棄する場合もある。導入から15年、20年も経過していれば決断は難しくないだろう。しかし5年も経っていないと鈍るのではないだろうか。この問題は導入時に遡る。特定の機能しか持たない専用機を入れると、入れた時には大きな効果が出るが、いざ転用しようとした時に大きな改造費用が掛かったり、場合に因って改造しても転用出来ない事が分かり、已む無く廃棄処分となることに。費用対効果が高く投資費用回収も楽、短期間で元手が取れ、利益が出る夢のような案件で有れば、専用機の導入も有りだと思う。ところが見込みが外れる事は普通に起こり、宝の持ち腐れというか経営的にも頭の痛い問題となる。導入を検討する場合、汎用性の高い設備、装置で対応出来ないか是非検討すべきである。
とはいえ、現実目の前にほぼ使用しなくなった設備があれば、一旦据え付け場所から撤去移動し、その空いたスペースを活用すべきである。活用方法が無くても空きスペースを作り、営業ツールの一つとして、いつでも増産、新規案件導入出来る事をアピールすべきである。廃棄・除却に掛かる費用が有れば適切に処理を行い、早期に社内から搬出し処分した方が良い。廃棄予定設備を保管していても何か得られる訳ではない。
大型の設備、装置以外の小物といった工具類に関しては、前述した設備と同じように専用工具は極力避け、汎用性、転用の利くタイプを選択し、長く使用出来るようにする。また、使用している間に摩耗、損傷等で本来の目的に適わなくなったら交換、「要らないモノ」として捨てる。勿体無いからと、不自然な使い方をして事故を起こすよりはマシである。
整頓:置き場所と置き方を決め、いつでも使えるようにする。
大型の設備配置は日常の活動で取り組むというより、事業計画で決め固定する場合があるので、ここでは生産活動で使用される工具等(小型の装置、計測機器を含む)が対象になります。
生産工程で使用する工具等は、一般的に作業手順書、組立基準書等に基づき作業エリアに置くようになっている。使用しない時には所定の場所(棚など)に戻し収納。使いもしない工具を作業者が勝手に持ってきて手元に置くことは無い(はずである)。しかし、生産機種変更後、計画上生産が無い時等、必要以外のモノを作業エリアに置きっ放しというケースがある。部品、材料、計測器にしても然り。このような現場でよく見られるのは「後で」と言い放置してしまう事。次のモノを準備するのは当たり前として、使い終わったモノ、この場で不要なモノまで置かれている。整頓だけでなく整理も理解出来ていない、出来ていないから「後で」が常態化する。汎用性のある工具(ニッパー、ペンチ、ドライバー等)だと、誰かが勝手に持っていき、返却忘れ等で紛失する事もよくある。生産に使用する為に準備した工具が紛失すれば、生産に支障を来し大きなロスにつながる。
作業中の置き場所、置き方は、組立作業の邪魔にならないよう、また床に落としたりしないよう専用のトレイかボックスを準備し、作業テーブル、床に直接置く事は避けるべきである。加えて、工具の保護と製品に傷を付け無いような置き方をしなくてはならない。一方、使用しない時は作業テーブル上から撤収し、棚かキャビネット等場所を決めて収納する。持ち出した工具等の場所には「いつ」「だれが」「どこに」が分かるカードを置く。見える化=可視化する事により、探すムダが無くなる。やりがちなのは、組立てを行う作業者よりも作業をサポートする担当、リーダー等が忙しさに紛れて放置したり、決められた場所に収納せず、次使用する時に探すムダを作ってしまう。任せっ放しにせず、管理者が気付いたらそれこそ「後で」ではなく、その場で指導し理解させるべきである。「後で」の文化は管理者の指導次第で改善されるものである。また、管理者が常時張り付いて見ていられる訳ではないので、習慣として動ける集団を育成する仕組み作りが重要である。言われなくても出来てこそ文化となる。根付くまで年間目標の一つとして、その達成度合いを測るのも良いかと。いわゆるP-D-C-Aを回して定着を図る、ということです。*PDCA:Plan、Do、Check、Action*
清掃:ゴミ、埃、汚れの無いようキレイな状態にする
組立作業で使用する設備、工具等はキレイな作業ばかりではなく、製品に因っては化学品、油脂類を使用する。使用している間に設備、工具等に付着、時にはキャップの締め方が悪く大量に漏れ出す事もある。そうした状態を放置せず拭き取る等掃除を行えば、それ以上の問題に発展する事は無い。状況次第で設備保全担当に連絡し適切な処置をしてもらう。計画数に影響が出るようであっても、生産を止めて処置をする方が後々の為になる。そもそも汚れが付着する、漏れる事自体が異常な訳で、掃除をせず無理して使用しても更なる問題を引き起こす。こうした状況に於いても「後で」は禁物である。問題を先延ばししたところで得るものより失うものの方が大きい。
こうした異常時だけではなく、清掃は平時問題の無い状態でも定期的に行う事で、異常の早期発見の役割がある。ゴミ、埃、汚れが無くても手順とタイミングを決めて(毎日同じ時間帯が重要)キレイにする。ただ掃除の動作だけではなく、キレイにする前と後の状態を目視は勿論、手で触った感触等変化が無いかを確認する。回転、摺動部に関しては、特に金属粉始めとする粉状の汚れが見られた際には、不具合が潜んでいる可能性が高いので必ず報告事項にすべきである。動かした時の音も重要なので、清掃は五感を働かせる作業と言っても良い。
工具等についても使用する・しないに関係なく、手順とタイミングを決めてキレイにする事は重要である。実物を見て、手で触れて作業に使用出来る状態なのかを確認する為である。見た目は同じでも、固定しているネジが緩んで生産時に使えないだけならまだしも、その事で製品にダメージを与えたり、作業者が事故に遭うといった問題の発生を予防する事にもなる。
キレイにする作業も大事であるが、作業に使用する用具、用品もキレイである事は重要であるし、サイズ、材質に付いても適切なモノを選ばないと、汚れを広げるだけでキレイにする目的は果たせない。サイズ、材質選びでは使用する対象、場所、頻度を考え選定する。油脂類の汚れが付き易い箇所に化繊系の吸い取り難い材質だと、拭き取るどころか汚れを広げるだけになってしまう事が多い。作業テーブルの拭き掃除用にレンズ、楽器等のクリーニングペーパーを使用したのでは、キレイになりはすれど、費用が掛かり過ぎる。コスパも含め適材適所の用具、用品を選定すればいいと思う。
5Sに熱心な職場は、掃除用具、用品自体もキレイにしているものである。ホウキの先が揃っている、モップは定期的に洗濯され黒ずんでいない、ちり取り、バケツもキレイ、キレイな掃除用具が整然と収納されている。用具、用品をキレイに使用している職場は、収納しているキャビネットの中、上なんかも埃の無いキレイな状態である。5Sが出来ていない職場は、掃除用具、用品と収納しているキャビネットを見れば程度が知れる。
清潔=整理、整頓、清掃が行き届き、いつでも使える状態にする
これまでの整理、整頓、清掃、いわゆる3Sの状態を保ち、問題無く使用出来る状態を言う。設備等については見て直ぐに分かり難いが、品質、納期がしっかりしている工場は5Sにも真面目に取り組み、成果を出している所が多い。
5Sの成果というのは3Sを実行する事で出る。3Sが行き届いている場所に居るのは気持ちの良いものである。職場に限らず個人宅でも、誰もが感じるはずなので、3Sをを継続させるだけで済む話であるが・・・
躾=整理から清潔まで習慣化し維持できる状態にする
整理、整頓、清掃の3Sは、指示する方もされた方も作業の一環だと思えば惰性で出来なくもない。やれば一応清潔な状態に出来る。しかし、3Sの意味と意義を理解して行うのとでは効果が全く異なる。3Sの意味と意義を理解していれば、掃除をするにしても、何かを追い求める姿勢になる。漠然と汚れを取り除くのではなく、なぜ汚れたのか、なぜ同じ個所に、同じ汚れが付くのか、汚れに対する探究心、3Sに対する目的意識を持つようになる。職場が清潔な状態を維持するには、指示を受け「やらされる」のではなく、自ら「やる」思考にしなくてはならない。躾を分解すると身と美になる。美しさを身に付ける。身だしなみを美しくする。どちらにしても、自分自身が心掛けなければ身に付かないものであり、他人任せでは自分のものにはならない。
調達先の生産現場を訪問する機会が数多くあった。設備・装置を使用している現場と、それらのメンテナンスを担当するエンジニアを注意深く見るようにしていた。それらが清潔な印象だと安心する。逆に設備周辺に工具が放置され、エンジニアのユニフォーム、手が汚れているのは設備に何か問題を抱えている証と考えていた。設備停止して納期が間に合わなかった場合、時々内容と対策時間に見合わない、合理性が感じられない事がある。修繕時間よりも有るはずの工具が見当たらず、工具探しに時間を費やし、仕舞には紛失していた為に、工具を新たに入手するまで生産が止まった。修繕時間はわずか数分であるが、一日止めてしまった事例もあった。それを反省し3Sに真面目に取り組んでもらえればいいのだが、得てして現場の担当はそれで仕事をしているつもりでいて、ムダな時間を過ごし残業になっても、むしろ作業者より仕事しているという勘違いをする。会社にしてみれば、やることやらずに、ムダなコストを掛けているのだから搾取とまで言わぬが、どうにかしたい思いになってしまう。エンジニアに限らず間接部門の人間は得てして似たような感じである。作業員は指示された事を行うので5Sを進めるには問題は大きくない。問題は、間接部門の人間に如何に3Sを理解させ、自発的な取組みとして定着させるか、難しい事では無い、経営者、管理者が諦めずに継続する姿勢を示し、5Sいや3Sをやり切る覚悟を見せる。それだけだと思う。

Exif_JPEG_PICTURE
Material:材料、Method:方法については次回。